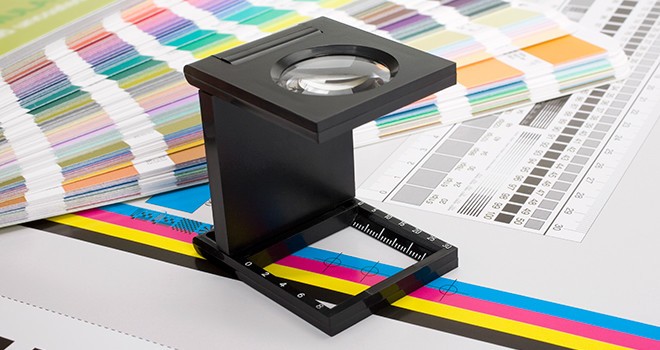
Press checking (or a press check), is a crucial step in the printing process where the designer (and/or sometimes client) physically inspects the printed materials as they come off the printing press. The purpose of a press check is to ensure that the final printed product meets the desired quality standards and accurately represents the original design.
Though a designer is not the one physically going about the printing process, it is important for them to be familiar with the terminology, as to make the press-checking process smoother and to have a higher level of professionalism. Here are a few helpful vocabulary terms and tips for when going about completing a press check.
Press Check Terminology
Here is a helpful list of phrases and terminology to know when completing a press check.
- Makeready: The process of preparing a printing press for a specific job. This involves adjusting settings, loading materials, and ensuring everything is in place before printing begins.
- Work and turn: A printing technique where one side of the sheet is printed, then the sheet is flipped or turned over to print the other side. This ensures proper alignment and registration.
- Work and flop: Similar to work and turn, but instead of flipping the sheet, it’s flipped along its horizontal axis before printing the second side.
- Take off bars: Bars added to a printing plate or image carrier to aid in the removal of sheets as they come off the press.
- Coverage: The amount of ink applied to a printed surface, often expressed as a percentage of the total area covered by ink.
- Densities: The darkness or lightness of printed areas, typically measured with a densitometer. Different densities can affect color accuracy and overall print quality.
- Proofing: The process of producing a sample or proof of a print job before full production. This allows for review and adjustments before committing to the final print run.
- Checking crossovers: Reviewing and ensuring proper alignment and registration of colors where they overlap or “cross over” each other in the printing process.
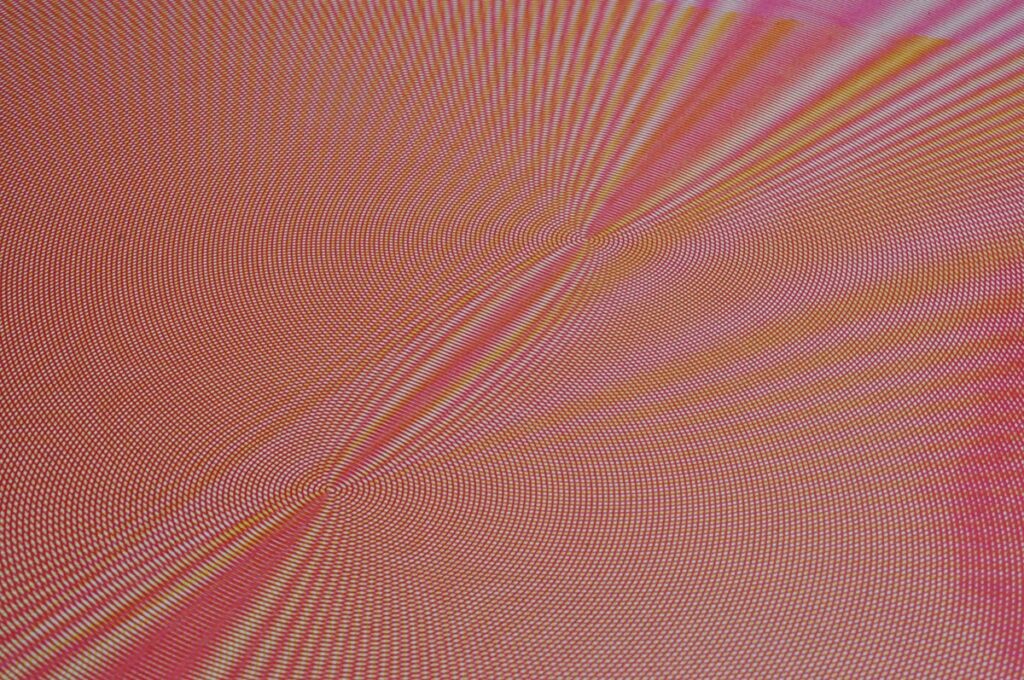
- Moiré patterns: Undesirable interference patterns that occur when two regular patterns (such as halftone screens) are overlaid improperly during printing.
- Color register: The alignment of different ink colors on a printed piece. Proper color register ensures that colors appear in the correct positions and don’t overlap incorrectly.
- Pinholes: Small holes or voids in printed areas caused by various factors, such as air bubbles or debris on the printing plate.
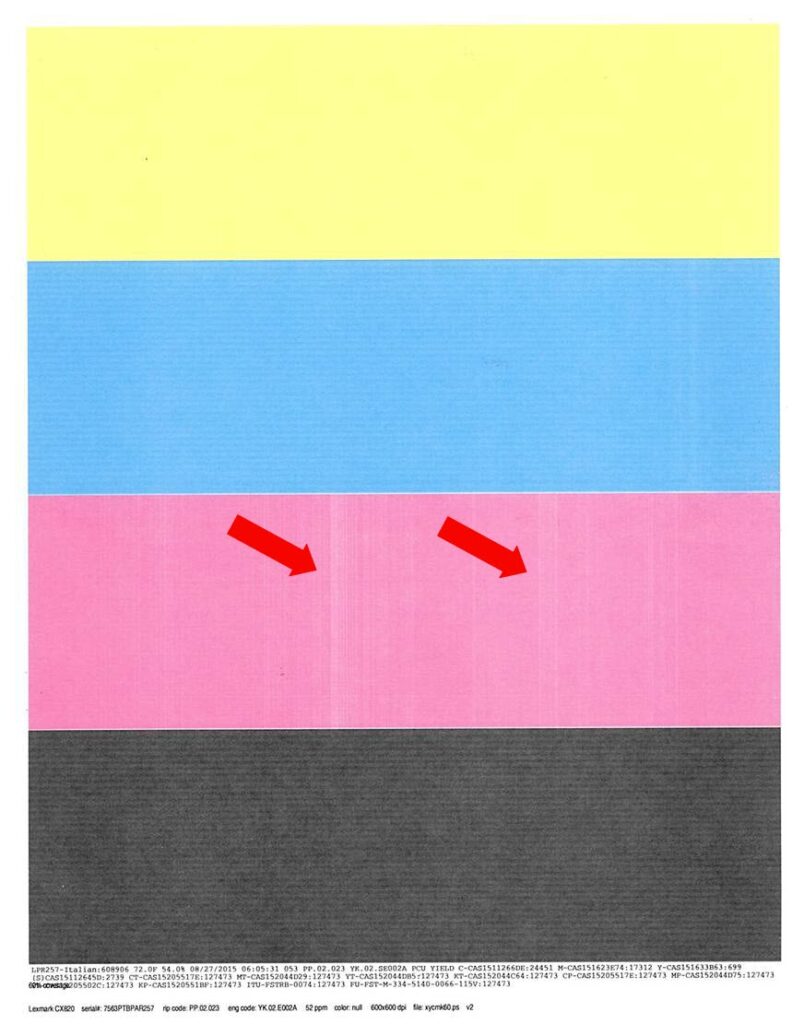
- Streaking: Uneven distribution of ink on the printed surface, resulting in visible streaks or lines.
- Imposition: The arrangement of pages on a printing plate or press sheet in the correct order for folding and binding after printing.
- Hickeys: Spots or imperfections in printed areas caused by foreign particles (such as dust) on the printing plate or press.
- Scum: Undesirable areas of ink buildup on a printing plate or press, often leading to blurred or smeared print.
- Broken type: Printing defects caused by damaged or improperly set type, resulting in incomplete or distorted characters.
- Signing a press sheet: The process of approving a printed sheet during a press check by signing off on its quality and accuracy before proceeding with the full print run.
Tips & Tricks
Along with this helpful list of press check terminology, here are a few helpful tips and tricks to keep in mind when completing a press check.
- Confirm the schedule: Double-check the press schedule to ensure that your press check aligns with the printing timeline. Confirming the schedule helps prevent delays and ensures that the press is ready for your inspection.
- Learn the Pressman’s Name: Build a relationship with the press operator! Knowing their name and communicating with them directly can facilitate smoother communication and collaboration during the press check.
- Bring essential tools: Apart from a lupe (magnifying glass) for detailed inspection, consider bringing earplugs to block out noise from the press. Some pressrooms can be loud, and ear protection can make the process more comfortable. Additionally, bringing a small pillow for back support during extended press checks can be beneficial.
- Look for moiré patterns: Keep an eye out for moiré patterns, especially in areas with fine details or patterns, such as fabric or clothing images. Adjustments may be needed to prevent or minimize these unwanted visual artifacts.
- Prepare contact information: Have contact numbers readily available for the client, print representative, and any other relevant parties. This ensures quick communication in case of any issues or questions during the press check.
By learning essential press-check terminology and following these tips, you can make the best of your press checking experience and ensure the successful production of your product!